Ever wonder how windshields are made? We did. So we wrote about it.
How is Auto Glass Made?
Windshields are a very familiar part of a vehicle. They act as safeguards for passengers protecting them from weather and debris. They create an aerodynamic element while providing comfort and functionality. They keep the vehicle roof from buckling during a rollover. And through it, the driver and front seat passenger can view the road ahead. Can you imagine life without windshields? We can’t either so let’s explore how automobile windshields are made.
Raw Materials of Glass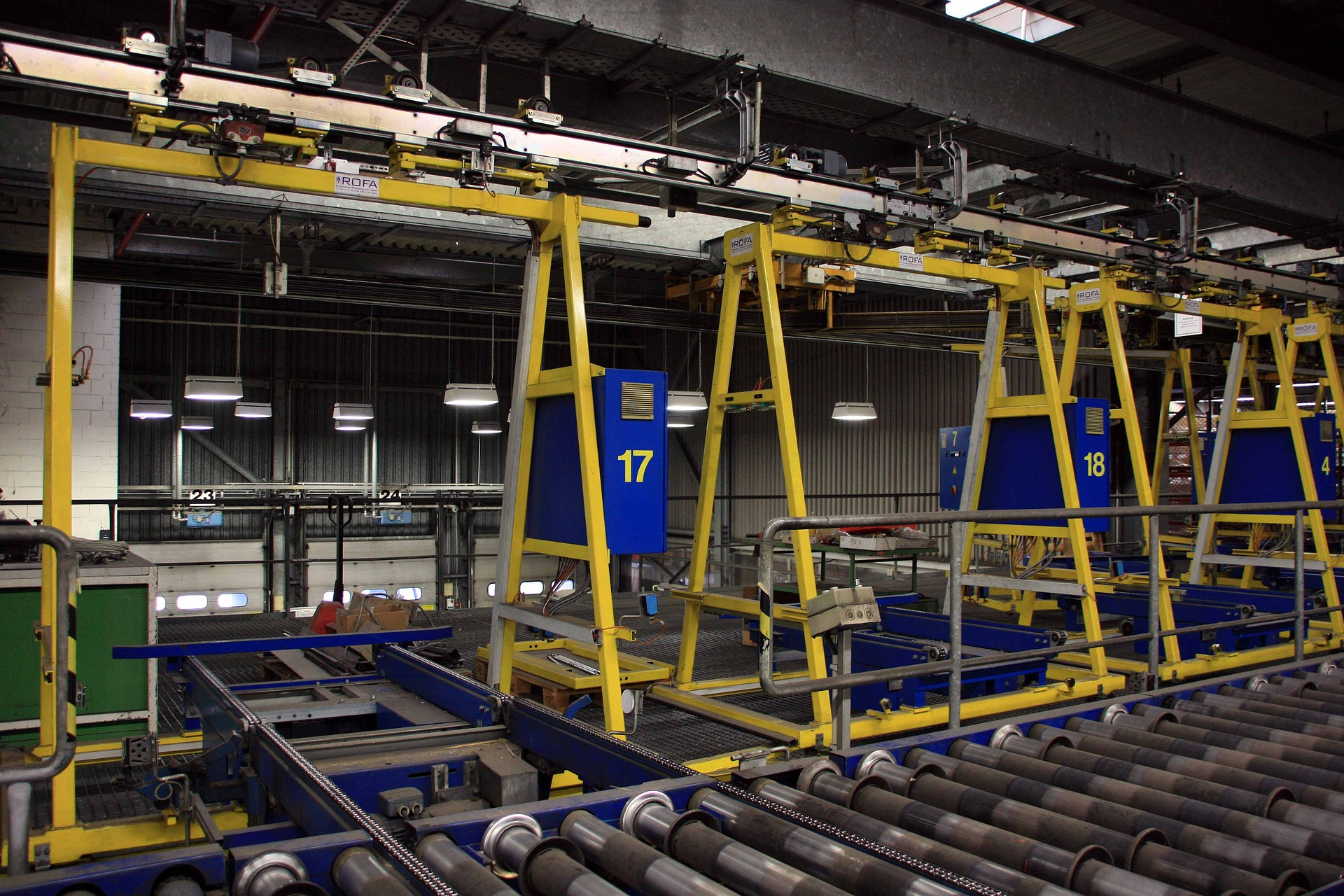
Glass is composed of oxides that fuse and react together when heated. The main ingredients are:
- Sand or Silica: Silicon dioxide is a chemical compound that is also known as silica and it is a type of sand that mostly consists of tiny granules of quartz. Silica has a very high melting point that is over 2,000° C and comprises about 60 to 70 percent of the windshield.
- Sodium Carbonate: When mixed with silica, sodium carbonate lowers the melting point to about 1,000° C which makes the glass-making process more efficient. Sodium Carbonate, however, causes the finished glass to be water-soluble.
- Lime or Calcium Oxide: Typically extracted from limestone, lime or calcium oxide counters the effects of Sodium Carbonate and makes the glass insoluble in water. Lime also improves the hardness and chemical durability of the glass.
- Potassium Oxide, Magnesium Oxide & Aluminum Oxide: Small quantities of these oxides are often added as well.
- Cullet: This is broken or waste glass that is added to facilitate melting in the making of new glass.
Add water, mix these ingredients together while heating them at a high temperature, and voila! The process of chemical fusion takes place giving birth to a new substance--glass.
Manufacturing Auto Glass
After the raw materials are properly measured in the appropriate amounts, the batch is melted using the float glass process. The “float method” received its name because the glass literally ‘floats’ inside a chamber during one of the manufacturing steps. This process produces a sheet of glass that has a uniform thickness and flat surfaces by floating molten glass on a bed of molten metal. In a specially designed float chamber, the glass floats as if it were moving through on a conveyor belt. At the opening, the temperature is about 1,000° C, which cleans the glass of any impurities. And at the exit, where it is 600° C, the cooler temperatures allow the glass to harden enough to move into the next phase of production.
After exiting the float chamber, special solar coatings may be applied. These coatings prevent heat from permeating your car interior in the summer while also retaining indoor warmth in the winter. The glass then enters a special furnace called a lehr where the glass is gradually cooled to about 200° C before cooling to room temperature when it is ready to be cut.
Cutting & Tempering of Auto Glass
After cooling, the large sheet of glass needs to be cut to size and shaped to its desired curvature. Using a diamond scribe, a cut line is made in the glass which is then broken or snapped. This step is automated to maintain high levels of accuracy. The sheet of glass is then placed into a mold where it is bent into shape. The glass-filled mold is heated in a furnace to the point where the glass fills the shape of the mold.
The glass is then tempered to improve its strength by quickly heating the glass and then blasting it with cold air. This process toughens the glass and puts the outer surface into compression and the inner surface into tension. By tempering, when the glass is damaged, the windshield will break into many small pieces of glass without sharp edges.
Auto Glass Lamination
The laminating process is where two sheets of glass are bonded together with a layer of plastic between them. This process takes place in a special oven called an autoclave where heat and pressure are used to form a single unit that is resistant to tearing. Lamination gives the glass strength as the glass will adhere to the internal tear-resistant plastic layer when broken. This also ensures good visibility because the plastic layer remains transparent even when the windshield is damaged. If a rock or piece of debris hits the windshield causing a chip or a crack, the damage is limited to the outside layer of the windshield. Imagine how dangerous driving would be if every rock or piece of debris could shatter the glass. Thankfully, glass lamination provides a much safer and more durable glass for our vehicles.
Additionally, different sensors, attachments, and moldings may be integrated or fabricated into the glass during the lamination process. These include everything from rain sensors to multi-use antennas to hydrophobic coatings.
Assembly
Finally, the windshield is ready to be assembled with plastic moldings so it can be installed on a vehicle. This process is usually done at a glass manufacturer where the glass is set in a mold cavity. Molten plastic is then injected into the mold and after cooling, a plastic frame is formed around the glass so the windshield can be shipped to a car or glass manufacturer.
Since windshield size and curve is dependent on the vehicles design specifications it is not advised to amend an existing windshield to fit a smaller vehicle. This would result in a poor fit and would compromise driver and passenger safety. It is always best to replace a windshield with a new one that fits the vehicle correctly according to manufacturer specifications. If you are in need of a windshield replacement or repair, Auto Glass Express is here to help. Our technicians are AGRSS certified by the Auto Glass Safety Council and we offer a lifetime warranty on all our work. Contact us and our mobile fleet of technicians will travel to you to get your windshield fixed today.